Quality Assurance
This improvement activity encompasses investment, technical, product and packaging development operations related to condiment manufacturing. Improvement is planned at the company and implemented using means regulated in procedures. Qualified and responsible workers are employed and external services of appropriate performance are used for and during planning and development work.
UNIVER Product Plc.’s corporate policy: Our goal is to play a decisive role on the market of typical Hungarian, traditional condiment pastes, mayonnaises, mustards, ketchup and salad dressings through profitable operation. Therefore, we have set the fundamental requirement of making safe products that meet customer expectations and statutory requirements in all regards, thereby bolstering our consumers’ confidence in and satisfaction with our products.
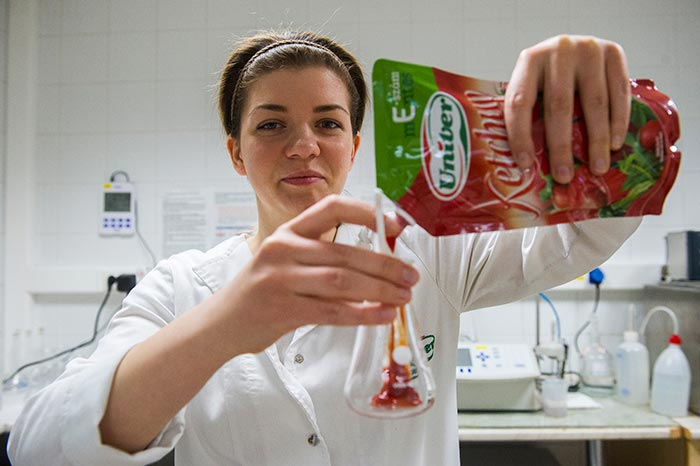
Applied methods:
To expedite our profitable operation, we operate a continuously audited and perfected, documented an ISO 9001, IFS standard compliant quality management system, with which we have integrated the HACCP system and an ISO 14001:2004 standard compliant environmental management system in the interest of food safety and protecting the environment.
Our employees are regularly informed and trained so that they can engage with the company’s quality targets and facilitate its achievement through continuously perfecting their work.
We are developing a regularly informed scope of suppliers that have the capacity to provide ingredients, raw and packaging materials, as well as services which comply with our quality targets.
We will continue to strengthen the recognized UNIVER brand, which expresses quality, on the market.
Our product range, production and packaging technology is continuously improved in line with market demands.
Our processes are analyzed and our competitors’ products monitored in the interest of preserving and boosting our competitiveness.
All of our company’s employees are committed to producing uniform quality, state-of-the-art and safe products that satisfy customer needs.
We firmly believe that the quality, food safety and environment protection aspects that take precedence in our thinking and practices increase confidence in our company’s activity and will lay the groundwork for our development in the future.
The Company’s corporate policy and quality management system addresses customers, learning and meeting their needs with priority, along with increasing customer satisfaction.
All of the Company’s executives have specified responsibilities in the interest of achieving our products’ declared quality targets.
The Company operates procedures which determine all of the activities that are required for us to accomplish our quality targets. The Company provides all the resources and HR criteria that are necessary for implementing our goals.
The Company sees to the efficient training and education of employees, and that they acquire sufficient experience.
In order to implement production and service delivery processes in harmony with objectives, the Company’s quality management system also addresses the specification of the necessary infrastructural and working environment related requirements.
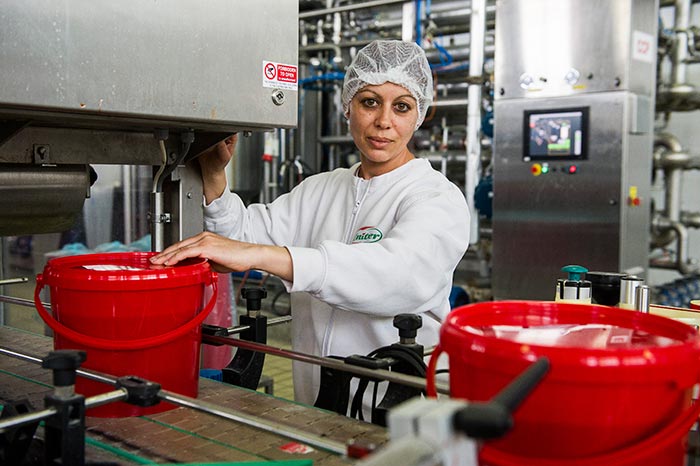
The Company regularly conducts analyses in line with the HACCP method with an eye to consumer safety and observing quality requirements.
UNIVER Product Plc. engages in continuous improvement in the interest of achieving its quality targets. This improvement activity encompasses investment, technical, product and packaging development operations related to condiment manufacturing. Improvement is planned at the company and implemented using means regulated in procedures. Qualified and responsible workers are employed and external services of appropriate performance are used for and during planning and development work. Statutory requirements and the demands of improvement targets are taken into consideration both during preparation and implementation steps in our improvement activity.
UNIVER Product Plc. seeks to order its purchased raw and packaging materials, and services from preliminarily approved suppliers in the course of its production and service delivery operations.
Accordingly, the Company assesses suppliers’ performance continuously in the interest of developing a reliable quality background.
The Company operates an appropriately documented system for identifying products and monitoring production processes.
Only materials and products that are declared satisfactory during validation testing may go on to be used.
The Company employs trained and responsible staff for conducting product quality control and documenting test results.